If you ask the investigator, ‘what caused the forklift accident in the warehouse?’ they will likely tell you it was operator error. Statistically speaking they’re correct. That does account for most accidents, but maybe the answer is too easy. What else could be going on?
Forklift operators have a lot more freedom and less supervision than other employees. Good operators become linchpins, integral to the smooth loading and unloading of merchandise. Bad operators are a nightmare that can hold up production lines or worse, hurt people. Yet, regardless of their training and experience, when accidents happen, there are always other factors.
Other Factors That Contribute To Forklift Accidents
Distracted and inattentive operators should probably be placed at the top of the list. The saddest part is that such mishaps are one hundred percent preventable.
When employees are rushed, frustrated, fatigued or work without awareness, their chances of making hazardous mistakes are greatly increased. It’s important for workers to recognize when their thoughts and emotions are eclipsing their safety. It’s also important for supervisors and safety professionals to know when to intervene or remind drivers to consider their state of mind.
Top 10 Forklift Accidents Video on YouTube
When it comes to forklift safety, properly training an employee on task-specific equipment before they get in the driver’s seat is mandatory, but not enough for long-term safety. As time passes, regulations change and equipment ages or gets replaced. More concerning is when employees become complacent about safety. All of these factors make refresher training a key component of a healthy workplace.
We assembled a list of factors which most commonly contribute to forklift accidents.
Forklift Operators Driving Too Fast

Forklifts traveling at excessive speeds may seem like a hyper-productive work environment, but unless the staff is incredibly well trained, they will crash someday and their speed will amplify the magnitude of the collision.
While driving too fast clearly falls into the operator error category, though some responsibility must be shared by supervisors who condoned the raceway and turned a blind eye to the developing situation.
While the US Department of Labor Occupational Safety & Health Administration (OSHA) doesn’t recommend a specific speed for forklift drivers, they do indicate that the responsibility is for the operator to drive within the employer-specified speed limit.
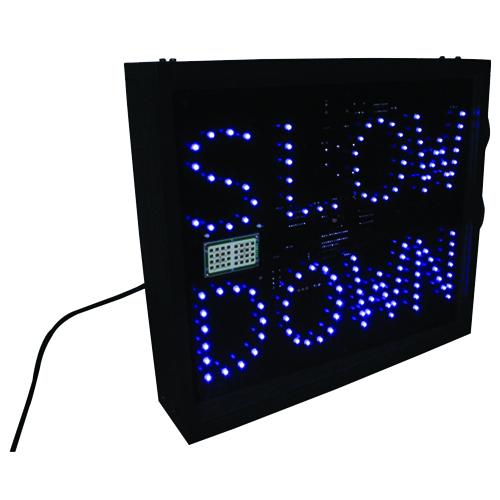
One remedy is to set speed limits and use a radar-operated forklift speed sign. Operators are alerted to SLOW DOWN when the unit senses vehicles moving over the set limit.
Forklifts Driving With The Load Elevated
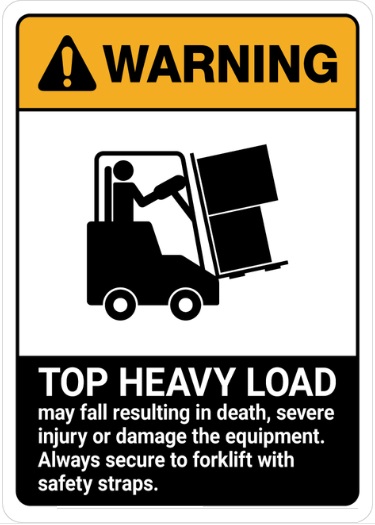
Traveling with a high center of gravity diminishes the equipment’s stability triangle and greatly increases the likelihood of tipping the load and possibly even upsetting the forklift.
A forklift has a three-point suspension system. The points are found over both of the two load (front) wheels and midway between the rear wheels. When imaginary lines are drawn to connect them, what’s known as the stability triangle is formed. Factors such as heavy loads or unbalanced loads, driving on sloping or uneven terrain, or turning with elevated loads can result in the center of gravity moving outside of the triangle. The result can be catastrophic.
The operator must ensure that the center of the load remains within the stability triangle to guard against tipping over.
Backing Up Forklifts In Busy Places
In some workplace environments with inclined planes and with certain models and equipment where the load blocks the driver’s view, operators are encouraged to drive in reverse. But be aware, according to OSHA (Occupational Safety and Health Administration), forklifts rank fourth in the number of fatalities caused by back-overs. Though OSHA does not require backup alarms on powered industrial trucks such as forklifts, they state, “certain operating conditions may require the use of additional warning devices, such as backup alarms.”
A smart business can protect itself and its employees from an unfortunate accident by purchasing a simple back-up alarm for forklifts or other powered industrial vehicles. There are even high-tech models that automatically adjust their sound level to be louder than ambient noise. Back-up cameras and of course mirrors are also worthy preventative options.
Improper Turning, Braking Or Accelerating Forklifts
Because forklifts carry loads up front, they need a heavy back-end counterweight for balance. Driving a forklift above the proper speed and then suddenly turning will likely ‘drift’ the rear end as the inertia carries the weight in direction traveled. This is clearly dangerous.
Since a forklift is turned by moving the rear wheels, it has a much smaller turning radius than a car. When cornering, the rear end swings outward. A forklift is also easier to tip over on a turn. The driver needs to be very careful when turning, stopping, or accelerating, since the vehicle could tip over, or the load could fall off.
Stunt driving forklift operators who are TikTok celebrity wannabes are downright dangerous. Dangerous for them and for the forty percent of forklift accidents in the USA involving pedestrians.
Lack Of Requisite Caution Signs For Forklifts
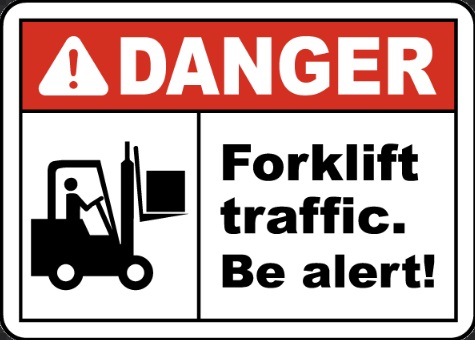
Accidents in warehouses are sometimes caused by pedestrians wandering into the path of forklifts who are not expecting them. Everyone is taken by surprise when such a calamity happens. Is it the fault of the driver, or the pedestrian? In most cases, it’s the floor manager’s fault for not posting proper warnings regarding the forklift in use nearby.
LED blue forklift safety lights can be installed to warn pedestrians of nearby forklifts and can also warn operators about another forklift that has entered their zone. When drivers spot the blue lights, they can tell from which direction another driver is coming, and it helps them navigate and avoid collisions.
Coordinated Forklifts Without A Coordinating Plan
Poor communication during shared tasks, or in shared spaces can lead to accidents. Sometimes a shared plan doesn’t have a proper contingency for bad weather, for traffic or for something unexpected happening on site. When operators and machines work together there can sometimes be misunderstandings that cause confusion and cause unsafe circumstances.
In the video that’s shared in this article there are a few examples where one group of workers doesn’t know or seem to realize what the forklift operator is doing until it’s too late.
Forklifts Ferrying Riders
Forklift operators who offer rides to other staff are simply asking for trouble. Unless the vehicle is designed to accommodate riders, which some personnel carriers are, forklift operators are causing passengers to take a very big risk when they step onboard to save themselves a walk.
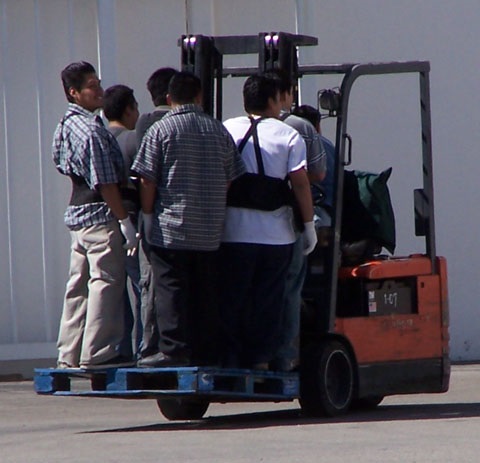
Compare a forklift to a car and you’ll recognize that these heavy machines are unique vehicles that present special challenges to drivers and afford no protection to riders. While the average automobile only weighs about 3,000 pounds, the average forklift weighs about 9,000 pounds. Also, forklifts are heavier in the rear to counter the weight of items being carried on the forks. And while cars have brakes on all four wheels, most forklifts only have stopping power in their front drive wheels. The rear counterweight and the front-wheel drive combined make the forklifts harder to stop, so they should be driven slowly. If the rider falls off the vehicle, then there is almost no way for the driver to stop in time to prevent them being crushed by the machine.
Forklift Parking Infractions Can Bring Deadly Fines
Forklifts that are improperly parked are just accidents waiting to happen. A forklift operator who gets out of a parked forklift that hasn’t been properly secured is in danger of being run over by his own vehicle. Similarly, a forklift that is parked on a ramp or incline without the parking brake being set could easily become a runaway train that weighs many thousands of pounds.
One of the first lessons of forklift safety is how to properly park a forklift.
Where the lift is parked matters. Gravity is one of the biggest dangers to forklift operators. Parking on a ramp, incline, or on an uneven surface can cause the forklift to roll down the slope. If the surface is steep enough, the vehicle’s parking brakes may not be enough to stop it from rolling.
Forklift drivers should test the parking brake on their machines to make sure it’s working properly by setting it, then putting the vehicle into either forward or reverse gear and stepping on the accelerator pedal slightly. If the vehicle doesn’t move, it’s safe. If it moves a little, try pushing the parking brake down further.
Unsafe Workplace Conditions For Forklifts
Some factors to consider here include improper blocking of wheels on semi-trailers or railway cars; this causes a lot of terrible accidents when platforms shift at exactly the wrong time. More obvious hazards are flooding, ice patches, gravel or tar on traveled surfaces. The danger of skidding when traveling on oil, grease, water or other spills rises with the size and viscosity of the errant substance.
Forklift operators in warehouses share a responsibility with other warehouse works to keep all aisles clear. If an area is cluttered, they should walk the route first to spot potential problems. Workplaces with overhead obstructions are problematic. When working outside in industrial areas, operators are trained to never drive straight across speed bumps or railroad tracks. Cross slowly at a 45-degree angle and to maintain steering control by keeping contact with the ground at all times.
Extreme weather can also impact the safety of an operation and in particular the forklift operators safety.
Read Forklift Safety In Wet And Windy Weather for more details and recommendations.
Forgetting Routine Forklift Maintenance
A routine and preventative maintenance schedule is crucial in identifying mechanical issues that could be hazardous, ensuring every truck’s continued safe operations and preserving financial investments. Maintenance should include a visual and operational pre-shift forklift inspections checks. Any forklift requiring maintenance should be immediately identified and depending on the severity of the issue, even be removed from service. By using the MasterCheck forklift inspection app, operators can quickly and easily check their machines. The aggregate of inspection data is accumulated on the Supervisor Dashboard and performance of forklifts and operators are easily analyzed by management.
The paperless MasterCheck app automates and simplifies the inspection process by providing operators with a quick and easy way to complete inspections from any type of device. The app remembers the operator and forklift information and quickly populates all identification fields. Operators then complete forklift inspections, repair reports, accident reports and near-miss reports, even including relevant photos, then simply click “send” to have the inspection sent to their supervisor and saved in the cloud.
All repair work performed on vehicles must be compliant with regulations and operators should not perform any repairs on the trucks unless they’re trained to do so. Additionally, no modifications should be made to a forklift if they’re not approved by the manufacturer. Always ask the forklift service provider to provide a written list of the maintenance being performed for your records.